What is GD&T
- Geometric Dimensioning and Tolerancing (GD&T) is a language of symbols and standards designed and used by engineers and manufacturers to explain a product and facilitate communication between entities working together to produce something.
- According to the ASME standard, the purpose of geometric dimensioning and tolerancing (GD&T) is to describe the engineering intent of parts and assemblies.
History of GD & T
- The origin of GD&T has been credited to a man named Stanley Parker, who in 1938 developed the concept of position called “true position”.
- Mr. Parker would later publish a book in 1956 entitled “Drawings and Dimensions”. Mr. Parker’s determination of position (or true position) has since grown to include other concepts including flatness, profile, runout, roundness and much more.
- The concept of GD&T was adopted by the military in the 1950s and is now GD&T use in multiple industries around the world.
Feature Control Frame
- Geometric dimensioning and tolerancing is applied on a drawing via one rectangular box called feature control frames.
- It’s a rectangle which is divided into small compartments within which geometric characteristic symbol, tolerance value, modifiers, and datum references are written.
- These feature control frames may attached below dimensions or at a datum reference or at a feature with a leader.
1. Leader Arrow - This arrow points to the feature or surface that the geometric control is placed on.
2. Geometric Symbol - This is where your geometric control is specified. Write the type of geometric tolerance.
3. Diameter Symbol (If Required) - If the geometric control is a diametrical tolerance then the diameter symbol (Ø) will be in front of the tolerance value.
4. Tolerance Value - It is the Tolerance value. The unit is the millimeter (mm).
5. Feature of Size or Tolerance Modifiers (if required) - Typical indications include (maximum material requirement), (least material requirement), and CZ (common [tolerance] zone) etc.
6. Primary Datum (if required) - The designer can specify as a datum the part that they want to prioritize as a reference. This is the datum that must be constrained first while measuring the part.
7. Secondary Datum (if required) - If a secondary datum is required, it will be to the right side of the primary datum.
8. Tertiary Datum (if required) - If a third datum is required, it will be to the right side of the secondary datum.
GD & T Tolerances are categories into 5 types
1. Form and Profile Tolerance
2. Orientation Tolerance
3. Location Tolerance
4. Run-out Tolerance
5. Associated Symbols
1. Form and Profile Tolerance
A. Flatness
- Flatness is a common symbol that references how flat a surface is with respect to any other datum’s or features.
- It is the condition of a surface having all elements are in one plane.
- Flatness tolerance is always less than the dimensional tolerance associated with it.
- Flatness symbol and indication is shown below
B. Straightness
- The straightness requirement specifies how perfectly straight a target should be.
- It is applied to lines and not planes and represents curve in the center line.
- Straightness is used to indicate the warpage tolerance of long objects.
- The standard form of surface straightness is a 2-Dimensional tolerance that is used to ensure that a part is uniform across a surface or feature.
- The form of straightness that controls the central axis of a 3D part like cylinder is sometimes referred to as Axial Straightness.
- Straightness symbol and indication shown below
C. Circularity or Roundness
- The circularity symbol is used to describe how close an object should be to a perfect circle.
- circularity is a 2D tolerance that controls the overall form of a circle ensuring it is not too oblong, square, or out of round.
- Circularity essentially makes a cross-section of a cylindrical or round feature and determines if the circle formed in that cross-section is round or not.
- Circularity symbol and indication shown below
D. Cylindricity
- The Cylindricity symbol is used to describe how close an object conforms to a perfect cylinder.
- Cylindricity is a 3-Dimensional tolerance that controls the overall profile of a cylindrical feature to ensure that it is round enough and straight enough along its axis.
- Cylindricity symbol and indication shown below
E. Profile of Plane
- Profile of plane describes a 3D tolerance zone around a surface usually which is an advanced curve or shape.
- Profile controls all the points along the surface within a tolerance range that directly mimics the designed profile.
- Any point on the surface would not be able to vary inside or outside by more than the surface profile tolerance.
- Profile of plane symbol and indication shown below
F. Profile of Line
- Profile of a line describes a tolerance zone around any line in any feature, usually of a curved shape.
- Profile of a line takes a cross section at any point along the surface and sets a tolerance zone on either side of the profile.
- Profile of line symbol and indication shown below
2. Orientation Tolerance
Orientation tolerances control the “tilt” of feature and are always associated with basic angle dimensions, If applied to surfaces, orientation tolerances also control form.
A. Perpendicularity
- Surface Perpendicularity is a tolerance that controls Perpendicularity between two Right angle surfaces, or features.
- Axis Perpendicularity is a tolerance that controls how perpendicular a specific axis needs to be with respect to a datum.
- Instead of degrees, millimeters are used as the unit for the value of perpendicularity indication.
- Perpendicularity symbol and indication shown below
B. Parallelism
- The parallelism requirement specifies that two lines or planes are parallel.
- Surface Parallelism is a tolerance that controls the parallelism between two surfaces or features.
- Axis Parallelism is a tolerance that controls how parallel a specific parts central axis needs to be with respect to a datum plane or axis.
- Parallelism symbol and indication shown below
C. Angularity
- Angularity is the symbol that describes the specific orientation of one feature to another at a referenced angle.
- The angularity specifies how accurate an angle is to the datum (reference plane or line) when the specified line or plane is not 90 degrees.
- Angularity does not directly control the angle of the referenced surface; it controls the envelope (like flatness) that the entire surface can lie.
- Instead of degrees, the millimeter is used as the unit for the value of angularity indication.
- Angularity symbol and indication shown below
3. Location Tolerance
Location tolerances control location and are always associated with basic linear dimensions. Position locates and orients the median plane or axis of features of size. Profile locates feature surfaces. Profile is the most powerful characteristic of all, and also controls orientation and form.A. Position
- Position Tolerance is how far your features location can vary from its “True Position / Mean Position”.
- Position is defined as the total permissible variation that a feature can have from its “Mean” position.
- Position symbol and indication shown below
B. Concentricity
- Concentricity, sometimes called coaxially, is a tolerance that controls the central axis of the referenced feature, to a datum axis.
- Concentricity is considered one of the most difficult GD&T symbols to measure for, due to its difficulty in establishing the midpoints of the feature.
- Concentricity symbol and indication shown below
C. Symmetry
- Symmetry is a 3-Dimensional tolerance that is used to check that two features on a part are uniform across a datum plane.
- Symmetry is not a very common GD&T since it has very limited functional uses (centering location is done with Position) and the verification and measurement of symmetry can be difficult.
- The symmetry specifies the accuracy of how symmetrical a target is to the datum (reference plane).
- Symmetry symbol and indication shown below
4. Run-out Tolerance
Run-out tolerance is a geometric tolerance that specifies the fluctuation of a target's feature when the target part is rotated on an axis (specified straight line). A datum is always necessary to indicate run-out toleranceA. Circular Run out
- Runout is how much one features vary with respect to another datum when the part is rotated 360° around the datum axis.
- It is essentially how much “wobble” occurs in the one part feature with referenced to another.
- To meet the circular run-out requirement, the run-out of the measured value when the part is rotated must be within the specified limit.
- Circular Run out symbol and indication shown below
B. Total Run out
- Total Runout is how much one entire feature or surface varies with respect to a datum when the part is rotated 360° around the datum axis.
- It controls circularity, straightness, coaxially, and taper of a cylindrical surface about a coaxial datum.
- Total Run out symbol and indication shown below
5. Associated Symbols
A. Envelope Requirement
- "E" Stands for Envelope.
- The envelope requirement means that the maximum (or minimum) allowable size of a component must be within the same range.
B. Free State
- It is a term used to describe distortion of a part after removal of forces applied during manufacture.
- Generally, geometric tolerance applies to rigid parts. For parts that deform beyond size tolerance or geometric tolerance in a free state, you will write "F" after the geometric tolerance in the feature control frame to indicate that the part is a non-rigid target.
- In below picture datum B must have a roundness within 5.0 mm, and the circular run-out on the left side is applied under restrained condition.
C. Least Material Condition
- The least material condition of a feature of size is the least amount of material within the stated limits of size. For example, the minimum shaft diameter or the maximum hole diameter.
- In below picture the position specification Φ0.5 is only applied when dia. 24 hole is in its least material condition Φ24.1
D. Maximum Material Condition
- The maximum material condition of a feature of size is the maximum amount of material within the stated limits of size, for example, the maximum shaft diameter or the minimum hole diameter.
- In below picture the position specification Φ0.5 is only applied when dia. 24 hole is in its Maximum material condition Φ23.9
E. Projected Tolerance Zone
- To indicate the projected tolerance zone, which applies to the range of the mating part, you write "P" after the value of the length of protrusion in the feature control frame.
- It controls the perpendicularity of the hole to the extent of the projection from the hole and as it relates to the mating part clearance.
- The projected tolerance zone extends above the surface of the part to the functional length of the pin, stud, and screw relative to its assembly with the mating part.
- In below picture the dia. 28 mm shaft center in the virtual space must be inside a dia. 0.5 mm cylinder throughout the entire length of the 30 mm protrusion of the dia. 28 mm cylinder whose axis is located 40 mm from datum B and perpendicular to datum A.
F. Theoretically Exact Dimension (TED)
- The theoretically exact dimensions are written in rectangular frames while the tolerances concerning that position are written in feature control frames.
- below picture shows the difference of Size tolerance indication and TED Indication
G. Datum Target
- A datum target is described using a circular frame with a horizontal line drawn through the middle (datum target frame).
- In the bottom half of the datum target frame, you write the letter/symbol indicating the same datum as that of the entire feature, along with the number of the datum target.
- Please see below picture
H. Spot Facing
- Cutting the entry point of a bore by a larger diameter for the purpose of making the surface smooth in order to prevent the heads of bolts and screws from protruding or to reinforce tightening.
- The below picture shows symbol of Spot facing
I. Statistical Tolerance
- Specification that assigns tolerance to the assembled components according to statistics.
- By applying statistical tolerance, the tolerance for each component can be increased, reducing the clearance between the components and the mating parts.
- this can improve product performance and/or reduce production costs.
- The below picture shows symbol of Statistical Tolerance
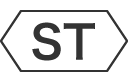
J. Unequally Disposed Profile Tolerance
- “U” stands for “unequally disposed profile.” This specifies the range of run-out of the offset amount from the tolerance zone (tolerance zone limit) in terms of the profile tolerance of a plane.
- A profile zone is presumed to be equally disposed around the perfect profile, but sometimes it is desired to have the zone be all to one side, or have a larger portion on one side than the other.
Post a Comment
Post a Comment
Please do not enter any spam link in the comment box.